by jeffp | May 19, 2016 | Construction
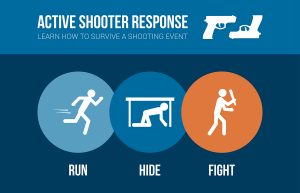
As defined by the Federal Bureau of Investigation (FBI), an active shooter is an individual who is actively engaged in killing or attempting to kill people in a confined and populated area. From 2000 to 2013, 160 active shooter incidents occurred in the U.S. This was an average of 11.4 incidents annually, and 70 percent of the incidents occurred in a commercial, business or educational environment.
In most cases, an active shooter incident ends in five minutes or less—before law enforcement can even respond. This means if you want to protect your construction workers, you must train them to identify potential warning signs of violence, raise their concerns, and make life or death decisions quickly should an active shooter incident occur at your office or on a jobsite.
Run, Hide or Fight
The FBI’s current model for responding to active shooters is to encourage civilians to run, hide or fight—in that order. Workers should be instructed to first run as far away from the situation as they can. If they are unable to get away to a safe location, they should locate a secure hiding place. In a heavily populated area, this may be a nearby building. In a remote location, it may be an onsite project trailer or a nearby stand of trees or bushes. Whatever hiding place is chosen, it should provide as much cover and protection as possible. Workers should never attempt to hide in a dangerous place, such as a roof or ledge without fall protection. As soon as it is safe to do so, the worker should contact emergency personnel with the location of the shooter as well as a physical description if known.
If the active shooter confronts the worker before he or she is able to run or hide, it’s time to fight. Train your workers to improvise weapons, act with aggression and take the shooter down as quickly as possible. A team approach—if other workers are nearby—may be more effective than an individual attack. Consider hiring a security company or Krav Maga instructor to provide self-defense training and run drills with your construction team as well as the teams of any subcontractors you’ve hired.
Create a Threat Response Team
The team should be composed of both management and non-management construction team members who will implement the emergency response protocols you’ve established for active shooter events. Train the team to provide information to local law enforcement in the event of an active shooter incident, provide first aid to anyone who has been wounded, and identify and search for missing workers who may have evacuated the jobsite. Inform your threat response team about all workplace violence complaints and concerns filed by your workers.
Raise Awareness of Suspicious Behavior
Train your construction workers to look for and report suspicious behavior that could indicate the potential for an active shooter or other workplace violence incident. These behaviors include threatening remarks or gestures, aggressive or hostile behavior, intentional destruction of property, self-destructive behavior and talk of violence. Talk of violence includes threatening social media posts.
Workers should also report any drastic changes in the performance of their teammates, signs of depression, or signs of paranoia. While such factors do not always mean a worker will engage in violent behavior, they may still pose other risks that should be addressed.
by jeffp | May 5, 2016 | Construction

While construction spending in the first two months of this year ($157.1 billion) was 11.2 percent higher than it was for the same period last year, and experts predict it will continue to grow at a modest pace due to low mortgage rates and increasing demand for new homes, volatility in other U.S. markets—as well as the world—hint at the potential for another recession.
Construction company owners—though most are cautiously optimistic—may remain focused on reducing operational costs as a result. While it’s generally wise to embrace strategies that result in meaningful financial savings—such as adjusting staffing levels and the use of new tools to improve efficiencies—keep in mind these risks you may not have considered.
Risk: Construction Labor Shortage
During the recession of 2008, the number of construction workers in the U.S. contracted. Many were forced to leave the industry in search of other work, and some contractors have struggled to meet labor demands ever since. This shortage of skilled workers has had a direct effect on workers’ compensation claims. Fewer construction professionals—many with little experience—working more hours can easily lead to more on-the-job accidents. By some estimates, short-staffed construction companies could see their accident-related losses increase at least 30 percent. This, in turn, will increase their workers compensation insurance premiums.
Risk: Design-Build Liability
Design-build construction projects are becoming increasingly prevalent as fewer nonresidential and residential builders continue to use the traditional design-bid-build contracting method. While this shift in business model has the benefit of increasing collaboration and productivity, it can also expose contractors to greater professional liability risks.
Contractors whose general liability insurance does not include protections for design work remain exposed even when that work is subcontracted to another entity. As such, it’s recommended that you close the professional liability gap by purchasing your own professional liability policy with conditional design coverage rather than rely on general liability coverage alone.
Risk: Cyber Security
Adoption of technology can help contractors improve services and meet bid requirements as well as streamline the workflow and reduce timelines. However, the more technology you use, the greater your cyber security risks. To minimize these risks and protect sensitive employee and project data, contractors and construction company owners should implement a cyber security risk management strategy. This includes evaluating your company’s current IT security, reducing the potential for breaches, and investing in cyber liability coverage.
Is your company fully protected from these risks? Give us a call today to discuss your current insurance policies and possible adjustments or additions to provide you with greater protection.
by jeffp | Apr 6, 2016 | Construction

If you’re a construction business owner, you know you need to have insurance in place to protect you from financial loss associated with construction projects. While many companies still go the traditional route—requiring each party to purchase their own policy—some are switching to an alternative method of risk management.
Known as a “wrap-up” or consolidated program, this approach allows the project owner to purchase a single policy to cover everyone involved—from the owner and construction manager to the general contractor and subcontractors. Wrap-up policies typically provide coverage for general liability, builder’s risk and workers’ compensation in addition to other features based on the type of project.
Owner controlled insurance programs (OCIP) and Contractor Controlled Insurance Programs (CCIP) are the most common types of wrap-up programs. Many of their advantages are the same:
- Cost Savings – Because you’re basically buying insurance in bulk, you can get coverage at a lower cost. This means the premium for the wrap-up insurance policy will be lower than the total of premiums purchased by individual contractors.
- Efficiency – Because a single insurer is handling all claims, processing is streamlined.
- Eliminates Duplication – When contractors and subcontractors purchase individual policies, coverage generally overlaps because they have to ensure themselves for the same accidents. This can lead to litigation between insurance companies in the event of a claim.
- Isolates and Reduces Risk – Wrap-up insurance allows the project owner to isolate construction risks from core operational risks. The owner can also ensure there are no gaps in general liability or workers’ compensation coverage and create a centralized safety program.
Of course, wrap-up programs also have their disadvantages:
- Administrative Costs – Because the project owner is responsible for purchasing wrap-up insurance, paying premiums and filing claims, he must provide administrative support. This may require an additional internal hire or outsourcing of administrative duties.
- Upfront Premiums – Some insurers require company owners to make a large upfront premium payment before the start of the construction project.
- Contractor Resistance – Some contractors and subcontractors prefer to purchase their own insurance. They like to include the cost in their bid and may even generate a profit if their insurance carrier gives them a rebate. Wrap-up insurance can also increase the administrative costs when wrap-up insurance is used because they have to work with a different insurance company than the one that handles the rest of their coverage.
- Excluded Risks – Some wrap-up policies exclude certain risks such as offsite work, damage to another contractor’s work and pollution cleanup. The coverage duration may also be shorter than that of an individual policy.
As with any insurance policy, should you choose to purchase a wrap-up program, making sure you understand what the policy covers and does not cover is essential. You should also ask your insurer to review all of the policies you have in place to look for potential gaps in coverage and other risks. For more information on your construction insurance policy options, give us a call.
by jeffp | Mar 23, 2016 | Construction

On a construction jobsite, safety is everyone’s responsibility. Rules established by the Occupational Safety and Health Administration (OSHA) state that every contractor, regardless of its role, has a non-transferable duty to protect its employees from all hazards—regardless of who created them. This means that a general contractor, a subcontractor acting as a general contractor, or a sole proprietor who has subbed out specialty work can receive an OSHA citation and fine if an employee under them is injured on the job.
When issuing a citation, an OSHA inspector first determines the role each employer fits into.
- The creating employer is the one who created the hazardous condition by violating an OSHA safety standard. OSHA will cite the creating employer even if they employees injured by or exposed to the hazard work for another employer on the jobsite.
- The exposing employer is the one whose employees were exposed to the hazard because the employer knew of and ignored the hazardous situation, failed to discover the hazardous situation, and failed to take steps necessary to protect its employees. These steps may include correcting the hazard, asking the creating employer to correct the hazard, and removing employees from the job.
- The correcting employer is also responsible for correcting the worksite hazards. Correcting employers are usually employers hired to install or maintain certain health or safety equipment or devices.
- The controlling employer is the jobsites general supervisor. The controlling employer has the authority to address and correct all safety issues and is therefore expected to do so.
If you’re going to be the controlling employer on the jobsite, you should have a safety management plan in place before you begin hiring subcontractors. Consider doing the following to reduce your chances of winding up with a costly OSHA fine:
- Include a provision in your subcontractor contract that states they are required to follow all OSHA safety standards while working on your jobsite.
- Require subcontractors to submit a copy of their safety manual and worker training materials along with injury and illness records before you hire them. Don’t subcontract work to employers with poor records or who have incomplete safety programs in place.
- Require every subcontractor you hire to produce a site-specific training programas well. Ask them to guarantee in writing that each of their workers will receive site-specific training before their first day on the jobsite.
- If second and third-tier subcontractors are used, make sure your subcontractors report them to you as well as require them to submit the same safety program and training documentation.
- If the subcontractor or its employees will be performing work six or more feet above lower levels, require proof of a fall protection plan as well as documentation showing all employees have received fall protection training.
- Require the subcontracts to prove they have workers compensation insurance in place for all of their employees.
- Host a safety orientation for all subcontractors and employees before the job begins. Require all subcontractors and their employees to wear hardhats and safety goggles on the jobsite.
With proper safety planning and subcontractor management, you can avoid exposure to costly OSHA citations. For more insight or advice on this or any other construction risk management topic, give us a call.
by jeffp | Mar 23, 2016 | Construction
On a construction jobsite, safety is everyone’s responsibility. Rules established by the Occupational Safety and Health Administration (OSHA) state that every contractor, regardless of its role, has a non-transferable duty to protect its employees from all hazards—regardless of who created them. This means that a general contractor, a subcontractor acting as a general contractor, or a sole proprietor who has subbed out specialty work can receive an OSHA citation and fine if an employee under them is injured on the job.
When issuing a citation, an OSHA inspector first determines the role each employer fits into.
- The creating employer is the one who created the hazardous condition by violating an OSHA safety standard. OSHA will cite the creating employer even if they employees injured by or exposed to the hazard work for another employer on the jobsite.
- The exposing employer is the one whose employees were exposed to the hazard because the employer knew of and ignored the hazardous situation, failed to discover the hazardous situation, and failed to take steps necessary to protect its employees. These steps may include correcting the hazard, asking the creating employer to correct the hazard, and removing employees from the job.
- The correcting employer is also responsible for correcting the worksite hazards. Correcting employers are usually employers hired to install or maintain certain health or safety equipment or devices.
- The controlling employer is the jobsites general supervisor. The controlling employer has the authority to address and correct all safety issues and is therefore expected to do so.
If you’re going to be the controlling employer on the jobsite, you should have a safety management plan in place before you begin hiring subcontractors. Consider doing the following to reduce your chances of winding up with a costly OSHA fine:
- Include a provision in your subcontractor contract that states they are required to follow all OSHA safety standards while working on your jobsite.
- Require subcontractors to submit a copy of their safety manual and worker training materials along with injury and illness records before you hire them. Don’t subcontract work to employers with poor records or who have incomplete safety programs in place.
- Require every subcontractor you hire to produce a site-specific training programas well. Ask them to guarantee in writing that each of their workers will receive site-specific training before their first day on the jobsite.
- If second and third-tier subcontractors are used, make sure your subcontractors report them to you as well as require them to submit the same safety program and training documentation.
- If the subcontractor or its employees will be performing work six or more feet above lower levels, require proof of a fall protection plan as well as documentation showing all employees have received fall protection training.
- Require the subcontracts to prove they have workers compensation insurance in place for all of their employees.
- Host a safety orientation for all subcontractors and employees before the job begins. Require all subcontractors and their employees to wear hardhats and safety goggles on the jobsite.
With proper safety planning and subcontractor management, you can avoid exposure to costly OSHA citations. For more insight or advice on this or any other construction risk management topic, give us a call.
by jeffp | Jan 28, 2016 | Construction

The Support of Management
Everyone in a position of authority—from the company owner to the job site supervisor—needs to put safety first and the project second. While most construction projects take place under tight deadlines, accidents are more likely to occur when workers are hurrying through their jobs, cutting safety corners along the way. The human and financial costs associated with the inevitable accident are significantly more expensive than the investment of time to follow protocol. Management must ensure that all workers understand this and perform their jobs accordingly.
Employee Education
Regardless of past experience, all new construction employees should be provided with appropriate training—from safety procedures to the equipment they will be using—before they’re turned loose on the jobsite. Supervisors should spend additional time supervising new employees as well. Seasoned workers can be valuable mentoring and teaching resources; use them wisely.
Tools and Equipment
Every tool and piece of equipment used on your jobsite should be in good condition, working properly and frequently checked for damages. Perform repairs immediately, and retire old equipment and tools when necessary. These rules apply to personal protective equipment (such as hardhats, harnesses, gloves, safety glasses and respirators) as well.
Work Zone Barriers
Whether your jobsite is in the middle of a city or the outskirts of the suburbs, utilize safety fencing or other barriers to keep unauthorized people out of the construction area. Additionally, use safety fencing to alert your construction workers to particularly dangerous areas within the jobsite (such as excavations and openings or locations where they may encounter falling objects).
Easy Access to Safety Materials
You can have the most elaborate job site safety plan in the world, the best-stocked first-aid kit, and oodles of equipment manuals and other documentation, but they won’t prevent even a single accident if they are not readily accessible. Designate spaces on your job site for safety materials and educate your workforce on how to access those materials.