by jeffp | Jan 15, 2016 | Construction
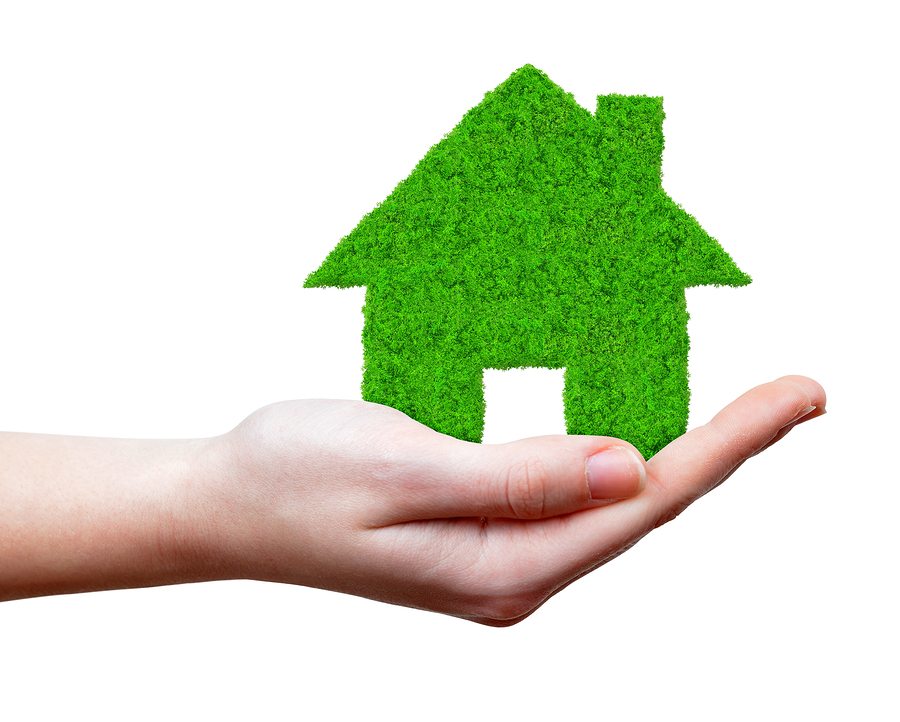
Energy efficiency, environmental sustainability, occupant health—these concerns and more are driving the green building trend and surge in U.S. Green Building Council LEED-certified structures. The council predicts total revenue across the eco-friendly construction industry will grow to $290 billion by 2017, and they intend to certify 1 million commercial buildings by 2020.
Unfortunately, the benefits that green construction provides building owners—including reduced operating expenses, higher asset value and a reputation for environmental stewardship—may come at a cost to construction employees. In fact, a study conducted by the Center for Construction Research and Training suggests that LEED-focused construction projects pose notably higher risks to workers.
Much of this risk comes from exposing workers on green construction projects to tasks and materials that are unfamiliar to them. For example, workers on LEED construction sites may have to work at height while installing solar panels and skylights. They may have to work with vegetated roofing materials and reflective roof membranes. The projects often require them to work with electrical current, near unstable soils and near heavy equipment for a greater period than they would on a traditional project.
Upon examination of the information gathered during the study—from site inspections and project documentation to job-hazard analysis and injury reports—the researchers determined that 14 LEED credentials could contribute to higher risks to construction employees. These included:
- Sustainable construction waste management – 36 percent increased risk of lacerations, strains and sprains
- Installation of photo voltaic panels – 24 percent increased risk of falls to a lower level
- Installation of reflective roof membranes – 19 percent increased risk of eyestrain
- Installation of green waste water technologies – 14 percent increased risk of exposure to harmful substances
While the U.S. Occupational Safety and Health Administration (OSHA) has yet to do so, the European Agency for Safety and Health at Work (EU-OSHA), issued specific green-building construction safety guidelines in 2013. They noted that green buildings are often tightly sealed and heavily insulated, increasing worker exposure to dust and dangerous compounds during construction. They also noted that green renovations present their own unique hazards, particularly worker encounters with fiberglass and rock wool insulation fibers.
Green building contractors can do the following to improve safety for their workers:
- Take the time to conduct a comprehensive hazard analysis before you begin any green construction project.
- Ensure you’ve trained all workers on the hazards they may encounter due to new materials or installation processes.
- Whenever possible, use low VOC materials to reduce health-related risks in enclosed environments.
- Decrease reflectivity by choosing tan or light gray roofing membranes rather than white. Alternatively, require your workers to wear tinted eyewear during installation.
- Ask designers to place photovoltaic panels closer to the ground or in the center of the roof. Consider higher parapets and designed tie-off points to reduce fall risk further.
- Enlist a local third-party waste management company to sort and recycle construction materials offsite.
Whether you’re a green construction veteran or considering your first eco-friendly project, make sure your risk management plan addresses the increased worker safety risks of green building. Consult your insurance professional for further insight and a plan review today.
by jeffp | Dec 28, 2015 | Construction

While the Occupational Safety and Health Administration (OSHA) has many rules in place to help employers reduce recognized hazards in their workplaces, the construction industry is particularly complicated. At any worksite, you may find multiple employers—from owners to general contractors to subcontractors—working simultaneously. In such a situation, it’s common for the actions of one company’s employees to affect the safety of the others.
For this reason, OSHA created the Multi-Employer Worksite Policy. It allows the issuance of citations to employers who endanger other contractors’ employees as well as those who expose their own workers to hazardous conditions.
Four Categories of Employers
According to OSHA, multi-employer worksites may contain employers from four categories.
- The controlling employer—in many cases, the acting general contractor—has the authority to correct hazardous jobsite conditions. As such, they are responsible for the safety of all workers, regardless of their actual employer.
- The creating employer is the employer whose activities have created a hazardous condition. The creating employer may be the general contractor, another contractor or a subcontractor.
- The correcting employer is the employer responsible for correcting the hazardous condition. This includes the creating employer and the general contractor, in many cases.
- The exposing employer is any employer whose workers were exposed to the hazardous condition. This may include every employer on the worksite, depending on the severity and nature of the hazard.
It’s not unusual for OHSA to issue a hazardous condition citation to every contractor and subcontractor on a multi-employer worksite, despite only one employer creating the hazard and union jurisdictional rules prohibiting members of one craft from correcting the hazards created by another.
Enhancing Worksite Safety as a General Contractor
While it’s important that each employer on a multi-employer worksite understands its role and responsibilities in eliminating safety hazards, the primary employer, general contractor or controlling employer can take additional steps to limit the likelihood of accidents, injuries and OSHA citations.
- Start with safety planning. Take the time to formally identify site-specific hazards, outline necessary safety precautions, and assign responsibilities to worksite employers. While you should always do this before starting a new project, you should also make updates before each new phase.
- Put it in writing. Include the worksite safety requirements you’ve outlined in every contractor and subcontractor contract.
- Review contractor/subcontractor safety records. When selecting contractors and subcontractors for a job, review their past OSHA citations, accidents and injuries, and safety practices. Never hire an employer with a poor safety history.
- Hold regular meetings. Whenever you begin a phase or bring in new contractors or subcontractors, hold a mandatory safety meeting in which you discuss the worksite specific safety plan and expectations for maintaining safe work conditions.
For best results, establish a clear chain of communication on worksite safety issues. If all contractors and subcontractors understand how to notify the appropriate party when they discover a hazard, it will be easier to deal with it properly and promptly, reducing the chance for accident or injury to any employers’ workers.
by jeffp | Dec 11, 2015 | Construction

According to the Occupational Safety and Health Administration (OSHA), 30 million people in the U.S. encounter hazardous noise levels on the job every year. Thousands of these workers suffer preventable Occupational Hearing Loss as a result. It’s an all too common and expensive occupational injury. In fact, hearing loss disability costs our nation an estimated $242 million annually in worker’s compensation according to the Centers for Disease Control and Prevention. While medical science is as yet unable to cure noise-induced hearing loss, employers can help to prevent it.
How Much Noise is Too Much?
OSHA recommendations include keeping workplace noise levels below 85 decibels (dBA) over an eight-hour time-weighted average. While research has indicated that regular, eight-hour exposures to 85-dBA noise can damage your workers’ hearing, higher noise levels cause damage even faster. For example, at 100 dBA, repeated exposures of as little as one hour per day can cause irreparable hearing loss.
Construction worksites are particularly noisy due to the equipment regularly used within them. For example, graders and scrapers produce noise at 107 dBA, jackhammers run at 102 dBA, and even bulldozers are as loud as 100 dBA. Concrete saws and electric grinders emit 98 dBA, while nail guns (97 dBA), forklifts (93 dBA) and belt sanders (90 dBA) also produce noise levels well above the OSHA recommended 85-dBA level.
What Can You Do?
One of the simplest ways to reduce hazardous noise exposure on your construction jobsite is to create a plan of attack before the project begins. This requires the general contractor, contractors and subcontractors to discuss activities and equipment use that is likely to generate hazardous noise as well as ways you can limit your employees’ exposure in addition to providing OSHA-required personal protective equipment. To get started, consider the following:
- Reduce Noise Levels – Whenever possible, choose the quietest equipment available. For example, one brand of generator may naturally produce fewer dBAs than another does. Proper maintenance is also essential. When you change seals, lubricate parts, replace blades and install mufflers, you can often reduce noise level production significantly.
- Move the Source – Noise level exposure goes down as you increase the distance between noisy equipment and your workers. Use extension cords, air hoses and other devices to move equipment farther away from wherever the main work area happens to be on a given day.
- Block the Noise – Construct temporary barriers out of plywood or other on-site materials and place them around your noisiest equipment. This will reduce the noise level exposure of other workers on the jobsite.
- Change the Schedule – Scheduling the loudest construction activities for times when the fewest number of workers are onsite is a very effective way to reduce hazardous noise exposure.
The National Institute for Occupational Safety and Health (NIOSH) recommends all employers implement a program for hearing loss prevention that includes noise assessments, engineering controls (such as acoustic barriers), audiometric monitoring, hearing protection equipment, worker education, record keeping and regular evaluation. You can find a number of resources on the OSHA website that should be of help regardless of your industry.
by jeffp | Nov 25, 2015 | Construction

Workers’ compensation premiums represent a major personnel expense for most organizations. Injuries that cause employees to miss work are especially costly, in terms of both lost wage compensation and lost productivity. Also, the longer a worker is disabled and unable to work, the more his future earning power decreases and the more likely it becomes that he will hire an attorney. For these reasons, it is advantageous to both employer and employee to get the injured worker back on the job as soon as possible. As a result, many employers have implemented return to work programs.
Under a return to work program, the injured employee performs a different job while receiving his prior level of pay. The new job should be matched to his current physical capability, reflecting his state of recovery from the injury.
To succeed, this requires a good working relationship between the employer and treating physician. The employer needs accurate information as to the tasks the worker can safely perform; otherwise, the result may be a second, more severe injury. If the worker’s physician will not cooperate or provide a realistic estimate, the employer or insurance company may have to require a physical examination by an independent physician.
A return to work program should be one piece of a comprehensive and coordinated loss management program. The elements of the program should include:
- Immediate reporting and investigation of accidents
- Arrangement of primary medical care
- Return to work program
- Regular communications with the injured worker
To assist in the arrangement of primary care, the employer should provide the treating physician with job descriptions that explain each job’s physical tasks in detail. Meetings with the physician to explain the nature of the employer’s operation will help match a job to the worker’s capabilities. Communications between the physician and the employer are vitally important. The employer may want to arrange for direct reports from the physician or regular reports delivered by the employee. The ideal situation is one where the employee can assume light duties without missing any time.
Barring that, limiting lost time to a week or two will still keep the claim’s cost down, resulting in premium savings for the employer. The experience modification formula, which adjusts the premium based on loss history, gives the most weight to losses of $5,000 or less.
Getting the injured worker back on the job quickly will help keep the loss well under that limit. Since losses remain in the calculation for three years, the effect of holding down claim costs is long lasting.
Of course, return to work programs have pros and cons. The pros include:
- Limiting or eliminating lost work time
- Keeping the worker involved in the work environment
- Eliminating the need to locate, hire and train a replacement
- Increasing the chances of success should the worker refuse the new duties and sue for lost wage benefits, since the employer can show that it made a reasonable job offer
Among the cons are:
- The employer will pay the employee’s full wage for reduced productivity
An employee with a bad attitude about his alternative duties could lower morale among the other employees
- If the alternative arrangement does not work out, returning the employee to lost wage benefits will wipe out any cost savings
- While individual cases might not produce the desired results, employers should realize long-term savings by implementing return to work programs. Beyond the verifiable dollar savings, return to work programs can give the employer a more stable, happier workforce and a good reputation with potential employees.
by jeffp | Nov 12, 2015 | Construction

Of events with negative financial and commercial impacts, natural disasters such as floods, hurricanes, tornadoes and earthquakes are at the top of the list. In 1907, a massive earthquake in San Francisco touched off a financial panic that nearly turned into a full-scale depression. Hurricane Katrina in 2005 cost an astounding $125 billion dollars in damages. The hurricane shut down nine oil refineries and another thirty oil drilling platforms.
Obviously, natural disasters can wreak havoc on all industries, not just oil and fishing. Small and large businesses are equally afraid of the effects a natural disaster will have upon their balance sheets. The inability to quickly recover from a disaster means certain death for the business. This is why having a disaster recovery plan is so important. The proper plan can help business owners get their operations back on track without permanent losses.
Needs Assessment
To formulate a disaster recovery plan, the business needs to first assess their needs. A qualified insurance agent can go over the books alongside the business owner and clearly state what requires coverage, such as loss of income, continuing operating expenses, or miscellaneous expenses after disaster strikes.
Document Organization
Organization is one of the most critical components to surviving a disaster intact. The right documents all gathered together and secured properly will save hundreds of hours later. Depending on the nature of the business and/or what industry it operates in, off-site backup of critical files may be called for.
Commonly, insurance companies will insure the basic constituents of a business, such as business income. Business interruption insurance will replace lost income as a result of the business being closed for whatever reason as the result of a disaster. This is why having documents organized properly is so important. The claims adjuster would need precise, detailed records of income and expenses in order to properly determine what the profits would have been had the business not closed due to disaster.
While it is next to impossible to determine what the document list should be for all businesses, here are some general documents to keep backups for:
insurance policy contracts
information on all of the bank accounts associated with the business
- leases
- income tax return forms for the last three years
- sales records
- inventory lists
It is also wise to make a list of all of the important people the business would have to contact in the event of disaster. This list includes bankers, landlords, accountants, creditors, employees, customers, etc.
Evacuation Plans
Preparing an evacuation plan will aid the business executives and employees by telling them exactly how to proceed during an emergency. When forming the evacuation plan, the business must make sure that all employees have designated assigned roles that they will follow; this will help organize their efforts and keep things under control.
When the Worst Happens
After a disaster occurs, it is important to carefully document the damage extensively. The business must inform their insurance company immediately that a disaster has occurred and that they have incurred damages and/or losses as a result. The business owners are responsible for the safety and well-being of all of their employees before, during and after the disaster. If the building where the business has been located has been damaged, get the building inspected.
The business owners must survey the damage carefully. Photograph and videotape all damaged areas everywhere, whether inside or outside the building. If necessary, they can make initial repairs to prevent even greater damage, such as boarding up windows and holes in the ceilings and walls. Once the adjuster and local authorities approve the claims application, than repair work can begin.
by jeffp | Oct 28, 2015 | Construction

One third of all work-related construction deaths involve falls according to the Occupational Safety and Health Administration (OSHA). In 2010, of the 774 fatalities recorded on construction jobsites, falls played a part in 264 of them. Workers who lost their lives included 90 who fell from roofs, 68 who tumbled off of ladders, and 37 who plummeted from scaffolds.
In an effort to reduce the number of jobsite fatalities resulting from falls, OSHA has partnered with the National Institute for Occupational Safety and Health (NIOSH) and the National Occupational Research Agenda (NORA) on a nationwide outreach campaign. Intended to raise construction employer and worker awareness of common fall hazards, the campaign provides a reminder of the simple steps anyone can take to prevent falls from roofs, ladders and scaffolds.
PLAN – Safety on the jobsite starts with careful planning. Contractors and subcontractors must evaluate the task at hand, determine how they will complete it, and ascertain what safety equipment is needed to do so. When bidding, employers should include safety equipment in their estimated costs to ensure they have the resources necessary to make life-saving tools—such as personal fall arrest systems—available to their workers.
PROVIDE – Falls from height carry the greatest risk of serious injury or death. To protect workers who are working six feet or more above lower levels, contractors and subcontractors must provide them with fall protection and the right equipment for the task at hand—from appropriate ladders and scaffolds to safety gear. All equipment should be regularly inspected to make sure it’s in good condition and safe to use.
TRAIN – Your workers must understand how to properly set-up and safely use construction equipment such as ladders, scaffolds and personal fall arrest systems. Training—for full-time, part-time and temporary or seasonal workers—is essential. Review these basics with your employees regularly:
- When using a ladder, ensure it has been placed on a level surface. Lock the metal braces at the center of the ladder before climbing it. Face the ladder when ascending or descending, and maintain three points of contact at all times. Never overreach or attempt to “walk” the ladder.
- When setting up a scaffold, ensure it is fully planked, all guardrails have been assembled, and the equipment is plumb and level. Have a competent worker inspect the scaffold before anyone uses it. Never climb over cross braces, stand on the guardrails, or attempt to use a ladder while on a scaffold.
- When working on a roof, always use a personal fall arrest system. Ensure all anchor points are safe and stay connected or tied off at all times. Cleary identify holes—such as openings and skylights—before roof work begins.
Many of those who are killed or injured on construction jobsites are temporary workers with limited English proficiency. OSHA downloadable training resources are available in multiple languages to help you ensure everyone on your team knows how to avoid life-threatening falls.