by jeffp | Jul 1, 2015 | Workplace Safety
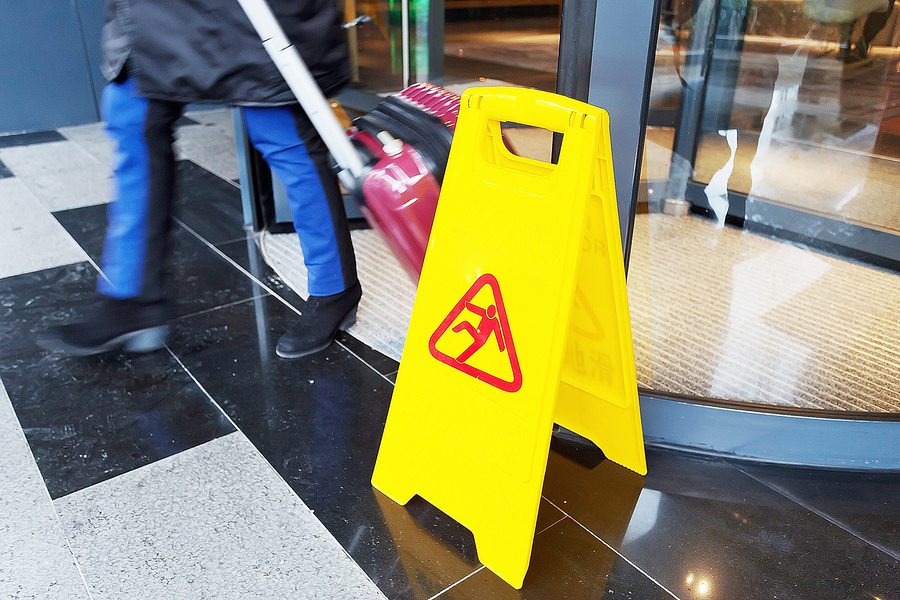
If you want to keep your employees safe, finding ways to eliminate the danger of slips, trips and falls will go a long way towards helping you do so. According to the Occupational Safety and Health Administration (OSHA), this nasty trio makes up the majority of general industry accidents each year. They also cause 15 percent of all accidental deaths. The only greater cause of fatalities is motor vehicles.
Walking and working surfaces generally play a part in slips, trips and falls regardless of industry. For this reason, the OSHA standards for walking/working surfaces apply to all permanent worksites with the exception of domestic, mining and agricultural locations. OSHA has standards employer can refer to for walking/working surfaces within general industries, shipyards, marine terminals, longshoring and construction.
Definitions
Before you begin to plan ways to prevent slips, trips and falls, it may be helpful to understand their definitions. According to OSHA, a slip is the result of too little friction between an employee’s footwear and the walking/working surface resulting in a loss of balance. Trips occur when a foot or lower leg is stopped by an object while the upper body continues moving, resulting in a loss of balance. Trips also occur with an unexpected step to a lower surface that causes a loss of balance.
There are two different types of falls, though both occur when your employee finds him or herself too far off center of balance. The first is a fall at the same level—defined as a fall to the same walking or working surface or against objects on the same surface. The second is a fall to a lower level, defined as a fall to a level below the walking/working surface.
Causes and Prevention
A common cause of slips is a wet walking/working surface due to spilled product or the presence of water, mud, dirt, grease or other fluids. If you keep surfaces free from all such forms of contamination, you’ll greatly reduce the incidence of slips.
Highly polished floors, freshly waxed surfaces and transitions from one type of walking surface to another (such as carpet to vinyl) can also cause slips. Make sure your cleaning crew is using appropriate cleaning products and processes that will not cause workplace slips.
Trips are often the result of objects that have placed in areas where they do not belong, such boxes in aisles or other clutter in walkways and work areas. Keep everything in its place and maintaining a neat and tidy workplace can reduce the incidence of trips.
Unmarked steps and ramps also cause trips, as do irregularities in walking surfaces. Use signs and other means to communicate visual warnings to your employees and worksite visitors. Track where trips occur in your workplace and eliminate walking surface transitions and irregularities if they are a regular source of incidents.
Poor lighting can increase the incidence of both trips and slips. Make sure your worksite is adequately lit and that you’re keeping lights clean. Lights that are covered in dust and dirt aren’t much better than no lights at all.
Stairway floor openings should all be guarded by standard railing on all sides (except entrance). Ladderway floor openings should also be guarded by railing. Pit and trapdoor floor openings should be guarded by covers and attended by someone when the cover is not in place. All of these measures can help prevent falls to a lower level.
Slips, trips and falls can reduce productivity and damage your company’s bottom line. Fortunately, most can be prevented with proper construction and implementation of a workplace safety program. Contact us today for a program review or additional assistance.
by jeffp | Jun 12, 2015 | Workplace Safety

It’s an unfortunate fact: workplace violence isn’t new. According to the Centers for Disease Control (CDC), 14,770 American workers became workplace homicide victims between 1992 and 2012. And recent data from the Occupational Safety and Health Administration (OSHA), Federal Bureau of Investigation (FBI) and Bureau of Labor Statistics (BLS) shows there were 397 workplace homicides in 2013 alone—accounting for about 9 percent of all workplace deaths. Four-fifths of these victims died from gunshot wounds.
While you may not think it will ever happen in your office, factory, warehouse or other place of business, the FBI reports that 45.6 percent of active shooter incidents occur in commercial areas. If that isn’t enough to spur you to include this threat in your workplace safety plan, perhaps a potential lawsuit is. Several victims of active shooters have successfully sued their employers for negligence in failing to provide defensive training to their employees. Refusing to address the threat of an active shooter in your workplace may even be a violation of the General Duty Clause of the Occupational Safety and Health Act.
Teach your staff to recognize the warning signs.
The most common type of active shooter encountered in the workplace is a current or former employee or friend/relative of a current or former employee. Warning signs exhibited ahead of time may include:
- Increasing belligerence, hypersensitivity or disorganization
- Unexplained radical changes in behavior
- Aggressive behavior such as pushing, yelling or threatening
- Obsession with a particular supervisor or coworker
- Anger at a particular supervisor or coworker
- On-the-job dispute with a supervisor or coworker
- Off-the-job difficulties such as bankruptcy or divorce
- Frequent mention of weapons or high-profile workplace violence incidents
Encourage your staff to report these signs to their supervisor, security or law enforcement as appropriate.
Teach your staff to protect themselves in an active shooter event.
Most active shooter situations are unpredictable, evolve quickly and last mere minutes. Experts advise teaching your staff to assess the situation and evacuate, shelter-in-place, or fight accordingly.
Evacuate – This should be the primary means of defense, provided there is an accessible escape path. Include escape routes from every department in your workplace safety plan and run frequent practice drills. In the event of an active shooter, your staff should be able to quickly evacuate the premises and call 911.
Shelter-in-Place – Sometimes evacuation is not possible and your staff will need to find a safe hiding place. Include potential hiding places in your workplace safety plan and run frequent practice drills. Hiding places should be out of the active shooter’s line of sight and be easy to evacuate if the situation changes. Hiding places that allow your staff to lock doors or blockade doors with heavy furniture are optimal.
Fight – While you should advise your staff to fight only as a last resort, you may want to provide them with training on simple ways to distract or incapacitate an active shooter. Tactics can include yelling, hand-to-hand self-defense techniques, throwing objects and improvising weapons.
Last but not least, you should make sure your staff knows what to do when police arrive. When evacuating the building, instruct them to leave personal items behind and keep their hands up and visible. They should promptly follow all instructions given by law enforcement and avoid making quick movements towards officers.
The Department of Homeland Security has created an informative booklet for employers and employees on responding to an active shooter. You can download it here. And remember, we’re only a phone call or email away if you’d like a workplace safety program review or additional assistance.
by jeffp | May 26, 2015 | Workplace Safety

Whether you’re in construction, manufacturing, transportation or any other industry, you know the importance of workplace safety, especially where the Occupational Safety and Health Administration is concerned. OSHA establishes safety standards and guidelines that all employers must follow or risk incurring fines and penalties. But there are more benefits to a safe workplace than just ensuring OSHA compliance. Consider the following hidden values many employers overlook.
Reduced costs from injuries
According to data from the Bureau of Labor Statistics, workers reported more than 3 million work-related injuries in 2013. The American Federation of Labor and Congress of Industrial Organizations say the BLS figure understates the problem. They put the total between 7.6 and 11.4 million incidents each year—costing employers $250 to $300 billion in direct and indirect losses. Fortunately, they also say that businesses that invest in effective workplace safety programs can save $4 to $6 for every $1 spent as illnesses, injuries and fatalities decline.
Lower worker’s compensation insurance costs
According to the Insurance Information Institute, businesses’ workers’ compensation insurance costs have increased substantially in previous years due to rising medical costs on claims. On top of these unavoidable adjustments, the number of claims paid against your policy will also raise your premiums. When you improve workplace safety, you minimize the chance of increases and may even reduce your costs. Reinvest your savings in additional safety measures and you can continue to keep costs low.
Increased worker productivity
According to OSHA, 4,585 workers were killed on the job in 2013. That’s almost 90 each week, or 13 preventable deaths every day. Such events can traumatize other employees, increasing workplace stress and absenteeism that reduces your company’s productivity and the quality of your product or service.
Of course, deaths aren’t the only issue. Injured employees may have to take medical leave, work shorter hours, or perform reduced duties. This, too, will reduce your company’s productivity. Fortunately, OSHA says businesses that implement effective safety programs operate more efficiently, reducing absenteeism, improving morale and boosting quality.
Lower car insurance premiums
Transportation incidents, including highway crashes, were one of the leading cause of workplace deaths in 2014. Company auto insurance premiums—much like personal auto insurance—increase with every accident. When you implement a workplace safety program that addresses transportation related dangers, you won’t just minimize accidents and protect your employees. You’ll also keep your company’s car insurance premiums low.
Better business reputation
You have a moral as well as legal obligation to protect your employees from accidents in the workplace. If your company develops a reputation for injuries or fatalities, it will affect your ability to attract top talent. It may also impact your chances of securing lucrative contracts and jobs from prospects that are familiar with your track record. When you implement an effective workplace safety program that goes above and beyond OSHA requirements, you protect that valuable reputation—and you can be certain your business will benefit.
by jeffp | May 12, 2015 | Workplace Safety

According to the U.S. Census Bureau, more than 60.6 million people speak a language other than English in their homes. Of those, 37.6 million speak Spanish. In fact, the U.S. has become the fifth largest Spanish speaking country on the planet.
The Occupational Safety and Health Administration (OSHA) has become increasingly concerned about the welfare of these non-English speaking workers, noting that immigrant Latino workers, in particular, have a 50 percent higher rate of death on the job. They’ve stepped up their protection efforts, repeatedly reminding employers that all workers much receive safety training in a language they can understand.
Employee comprehension is at the heart of OSHA’s policies. This means that all safety training must take into account the limited vocabulary of workers for whom English is a second language. It must also consider their level of literacy. For example, telling an illiterate worker to read a safety training manual—whether written in their native language or not—will not satisfy your obligation under OSHA rules.
Fortunately, OSHA offers assistance to employers with a Spanish-speaking workforce. Visit the Compliance Assistance Quick Start: Hispanic Outreach tool on the OSHA website to locate Spanish-language resources for compliance with the Occupational Safety and Health Act of 1970. You’ll also find links to OSHA’s English-to-Spanish and Spanish-to-English dictionaries that include more than 2,000 OSHA, general industry and construction industry terms.
Other measures you can take to ensure your staff understands the safety and health hazard information you’re presenting to them include:
- Use a translator – Hiring a translator to assist with the safety training of employees who speak limited English is less costly than the fines OSHA may impose should an inspector determine you have failed to meet the requirements for compliance.
- Demonstrate – When talking about proper safety procedures, demonstrate the actions required to complete them. You can also use visual aids such as illustrations to enhance comprehension.
- Practice – Have your employees practice safety procedures during the training session. This will allow you to access their comprehension and repeat your previous demonstration as needed.
In addition to verifying that employers have provided their workers with workplace safety training, OSHA inspectors are now making sure that training was provided in a language the employees could understand. They may do this by reviewing documentation as well as assessing your worker’s understanding of proper safety procedures. Should they determine workers were not trained using a language or manner they could comprehend, you may be cited with a serious OSHA violation.
by jeffp | Apr 23, 2015 | Workplace Safety

According to the National Council on Alcoholism and Drug Dependence, an estimated 8 percent of the U.S. population over the age of 12 has used illegal drugs in the last 30 days. Drug abuse costs employers $81 billion annually, causing increased absenteeism, carelessness and mistakes while decreasing safety and productivity. Given those figures, it’s easy to see why so many of America’s employers test their workers for illicit substances. However, far too few extend their caution to OTC and prescription medications. These drugs—while legal—can be equally dangerous in the workplace.
If you’d like to make sure your workers are using legal medications safely, you may want to include prescription and OTC medication use guidelines as part of your workplace safety program. Topics to address include:
Reading labels – If your employees are taking an OTC or prescription drug, they must read the label carefully. They should understand how the medication may potentially affect them, and look for warnings related to operating machinery and drowsiness or dizziness side effects. If the drug could affect their ability to perform work safely, they should notify a supervisor to discuss alternate assignments.
Testing prescriptions – Whenever a doctor prescribes a new drug for an employee, he or she should take the first dose at home, not at the workplace. Medications can cause different effects in different people—those listed on the label may not apply to everyone. The same goes for OTC drugs. Your workers should have a good understanding of how it will affect them before they take it on the job.
Avoiding interactions – Whenever an employee takes multiple medications in conjunction, drug interactions become a danger. Your workers should speak to their doctor or pharmacist before they take multiple medications or combine medications with herbal supplements. If effects that may impact their work performance are likely, they should seek alternatives or advise a supervisor.
Consider work conditions – Temperature and other factors can amplify the side effects of any particular medication. For example, if an OTC cold medication causes drowsiness, that drowsiness is likely to be more extreme if the employee has to work in heated conditions where sweating is common. If a prescription drug can cause headaches, it’s more likely to do so if the employee works in a fast-paced environment. Consider actual conditions when evaluating the safety of any prescription or OTC drug in the workplace.
By some calculations, nearly 70 percent of Americans take at least one prescription medication. More than 50 percent take at least two. These include antibiotics, antidepressants and opioid painkillers as well as medications for chronic medical conditions such as high blood pressure, diabetes and arthritis. Don’t let the use of prescription and OTC medication endanger your workforce. Contact us today for further assistance with addressing these issues in your workplace safety program.
by jeffp | Apr 10, 2015 | Workplace Safety
Every day, over 2,000 workers experience an eye injury that requires them to seek medical care, according to the National Safety Council. Although any worker can injure her eyes on the job, the majority of eye injuries occur in the construction, manufacturing, mining and agriculture industries. These accidents affect the quality of life of the people whose eyes are injured, and result in a significant amount of lost work time. Preventing these injuries is not difficult. Doing so requires having the right protective equipment on hand and insisting that workers follow eye protection procedures at all times.
Eye injuries are often caused by the following: flying particles from work materials, chemicals, falling objects, dust and UV light from welding torches. If your workplace exposes workers to any of these hazards, it is important that you have an eye-protection policy in place. Note that OSHA has specific standards for general industry as well as shipyard employment and construction.
Types of eye protection include safety glasses with side protection, goggles and face shields. The kind of protection you purchase for your employees depends on the type of work they do. For example, working in a dusty environment may simply require the use of safety glasses, while working with chemicals always requires that workers use goggles, while working with bloodborne pathogens will require the use of a face shield.
Sometimes, workers need to use task-specific eyewear that is appropriate to the work they will be performing, such as a welding helmet to protect the eyes from the intense UV light emitted by the arc. A person working with lasers will wear eye protection that has a special filter to protect his eyes from the light. It is critical that workers use the right type of protection for the task in order to prevent injury. This may mean that your company will need to purchase several different kinds of protective equipment for the eyes.
Note that any protective eyewear you buy must meet the ANSI eye and face protection standards. Appropriate eyewear will have Z87 marked on the frame or lens. Equipment should fit properly so that no space is between the glasses and the face that would permit flying debris to enter and cause injury. Maintain the equipment so that it performs properly, as scratched googles can be a hazard in and of themselves.
Taking these precautions should reduce the chances that any of your employees suffer from a serious eye injury. Refer to OSHA guidelines to ensure that your company meets all of the legal standards for eye protection.