by jeffp | Jul 11, 2017 | Workplace Safety

Because cannabis legalization is expanding across the United States, many companies are concerned about how to go about drug testing their employees. They are also quite concerned about workplace safety. (As you may know, cannabis or “pot” is legal in some form or another in 28 states as well as our capital, Washington DC.)
Each state’s laws regarding marijuana legalization are different, making it difficult for companies to know how to manage their employees when it comes to marijuana usage by employees and location.
(This can be especially tricky if a company has workers split between multiple states where some states offer legalization and others don’t. For example, Idaho does not offer pot legalization but is bordered by 3 states that allow legalization in some form or another.)
To help give guidance, here are some steps to leverage in order to keep the work environment accident free with the changing tide in pot regulations.
First, it is important to understand that public opinion towards marijuana has shifted in recent years. Today, approximately 60% of the population supports the legalization of cannabis. While this change may be thought of as coming from younger adults, the change in attitudes is actually most significant in the population age 55 and older. A current study found that in medical areas where marijuana was proven to be beneficial, Medicare enrollees were significant users of marijuana.
So what can companies do though if they have employees that use cannabis?
Of course, safety is a primary concern for these companies. It is important that companies concentrate on the efficiency of their employees in addition to increased scrutiny on training and hiring processes. (This is really no different than how alcohol is treated in the work environment.)
These four extra steps can help ensure a safe environment:
1. Review job descriptions and determine what each job requires. Would an employee who uses cannabis in non-working hours influence that person’s capability to perform essential job duties?
2. Train managers how to identify impairment caused by marijuana use in the workplace. Review signs and symptoms of a person who has used cannabis.
3. Determine if drug screening is a good fit for your business. If it is, determine how to best do it with your employees. For example at their time of hire or additionally throughout the worker’s employment.
4. Consider the impact medicinal marijuana may have on policies. For example, where pot use is truly necessary for a given worker’s medical needs rather than being a recreational choice.
Closing thoughts:
Research regarding marijuana usage indicates that the impacts of marijuana on a person’s ability to function changes drastically from user to user in addition to the type of work being done.
Of note, fewer than a third of studies found a relationship between marijuana use and reduced function.
For a complete understanding of how employee pot use may impact your safety risk profile, be sure to reach out to us for guidance. We’ll be sure to point you in the right direction.
by jeffp | Jun 8, 2017 | Workplace Safety

According to the American Federation of State, County as well as Community Staff members, one of the typical hazards associated with excavation or trenching job is cave-ins. Individuals bearing the highest risk of getting seized in a collapse include but not limited to:
a) Workers who repair utility lines like sewer, water, and others
b) Roadway building contractors and also
c) People who actively participate in digging.
Statistics by the American Federation Of State, County And Municipal Employees (AFSCME) indicate that slides or collapses during excavation can be instigated mainly by the following factors:
· The heavy weight of the excavation equipment especially if positioned near to the margin of a trench
· Loose soil culminating from construction equipment vibration and traffic in the construction location.
· Water accessing the construction site or the excavation location. This compromises the strength of trench peripheral and as a result a slide might occur.
· Loose soil that weakens the walls of the trench or construction and may end up collapsing.
Before performing any excavation or trenching activity, it’s always prudent to seek an expert to examine possible risks prior to commencement of the activity and also during the procedure till the process is complete. The operation ought to be regularly monitored in order to ensure that all possible hazards are kept on check.
On the other hand, protective measures have to be taken for any form of excavation or trench that happens to be deeper than 5′. However, digging operations that are fewer than 5′ deep might also require a safety system in case the professional onsite discerns a potential cave-in.
Below are some safety systems that are recommended in order to mitigate excavation and construction site hazards:
Shoring.
This system comprises of wales, cross-braces as well as uprights and needs to be installed from the top down as well as removed from all-time low up. It supports the wall surfaces of the excavation hence reducing the likelihood of a potential slide.
Sloping.
This system ensures the sides of the hole open out from the base of the excavation. This kind of soil management moves out an appropriate angle from the base (depending on the soil) to help prevent any probable collapse.
Shielding.
This system comprises of trench guards or trench boxes that are put in the digging site to prevent the trench walls from failing. The person is safeguarded while in the box. Some boxes can be moved as work progresses. All shields must protrude a minimum of 18 inches from the top of the trench slope.
Benching.
The benching system a lot like sloping. However steps are cut into the sides of the trench. It’s important to note that if you are digging more than 20′ deep you’ll need a registered engineer to authorize your solution.
Dealing With Risk Exposure
As a contractor you face many different kinds of risk exposure. It’s important to have comprehensive protection to be sure profits are preserved and that your company isn’t put at risk as a result of a catastrophic claim. Please reach out to us for cost-effective ideas on how to leverage and maximize insurance to limit exposure.
by jeffp | Jun 8, 2017 | Workplace Safety

Although most areas of the country have excellent fire departments, fires are still responsible for huge losses of jobs and lives. The most recent National Fire Defense Record (NFPA) record released in 2015 stated that there were more than 3000 civilian deaths and more than 15,000 fire injuries that took place in the United States. The costs associated with fires are more than $14.3 billion in home damage alone. The losses caused by fire affect not only personal homes and property, but also have an effect on work environments and businesses.
And while fire affects many businesses, it has a substantial impact on both small and medium-sized businesses who have fewer financial resources. These businesses are usually housed in a single location and, in the case of a fire, may not be able to continue their work. The key to preventing a loss of business is prevention and it’s every business’s job to keep the workplace safe from any potential fire threats. Fortunately, many of the fires that occur today are preventable.
These are just a few of the easy and effective ways to keep your workplace and your workers safe:
1. Keep the Office Clean
Having standards for the state of the workplace is an important step to prevent fire. Make sure to keep work spaces neat as any piles of waste and clutter are easy kindling for a growing fire. Make it a regular habit to get rid of any flammable materials such as wood and cardboard. Worker safety is a key element of prevention here so promote clean habits in the entire office. Make sure also to keep any waste baskets and dumpsters away from areas of heat.
It’s a common habit to destroy waste in an open pit or barrel, thinking that this is a safe way to get rid of waste. However, this is not only a fire hazard, but also illegal in most states. Instead of burning any trash, follow state and government guidelines to get rid of combustible waste safely. Look up the guidelines in the area and keep them posted in the workplace to inform all employees.
2. Watch for Potential Hazards
Potential fire spots are areas to watch out for in the office. There are a few key areas, for example, in the workplace which are specifically prone to fire risks. It’s important to keep an eye on them to prevent problems. For example, the kitchen is the most common place to experience a workplace fire. Coffee makers that have been left on can trigger a fire. Make sure to ask employees to turn off any appliances in the company kitchen before leaving the area. Also keep any flammable items away from appliances to decrease the fire risk.
3. Watch out for Faulty Wiring
Faulty electrical wiring is one of the leading violations according to the Occupational Security and Health Administration (OSHA) in 2016. Make sure that any cables and wires in use are in good condition with no exposed wires. It’s also important to use the appropriate power cable for the work. Substituting cords can be tempting in a pinch but can increase risk.
When using an electrical outlet, prevent any dual adaptor links. Instead, use a power strip with a fuse. Make sure to schedule regular electrical repair and maintenance to prevent any potential hazards. Additionally, it’s important for businesses to test any safety and security buttons roughly every three months. Keep in mind that electrical safety isn’t just based on the electrical system. Any water leaks in the building can also lead to blown circuits, fire, and personal harm. Water is a good conductor of electrical energy and can electrocute anyone in contact. Make sure that there are no water leaks in the workplace.
4. Use and Store Chemicals Securely
Most chemical cleaners and other materials are flammable. Make sure to read the label and security sheet on each container to determine if it is flammable and how best to use the product safely. All chemicals should be labelled correctly and stored based on the instructions. The chemicals should also be kept in secured containers when they are not in sure. Advise employees to only use their chemicals for their intended purpose. For example, ethyl alcohol should not be used to clean the floor or as a hand sanitizer. Provide employees with the appropriate equipment such as gloves and masks as well as any tools for dealing with hazardous chemicals. Clean up any chemical spills promptly and according to directions.
5. Screen Out Risky Workers
Although it’s a good idea to hang “no smoking” signs to let your employees know that smoking is not permitted and carry out regular fire drills, sometimes these steps aren’t enough to make your work environment safe from fire hazards. Each company takes a different approach to maximize workers safety and the safety of the environment. Industrial companies, for example, are starting to screen out potentially dangerous workers in their goal to create a safe and reliable work environment.
In the past few years, there has been a rise in pre-employment alcohol and drug tests. Many of these screening kits are easy for employers to use with potential employees. Make sure to use a kit that has been FDA-approved. These kits are a good way to determine if an employee engages in any risky behaviors which could increase the company’s risk of an accident or fire.
6. Prepare for Emergency Situations
Although using the steps above to prevent a fire is key, some accidents can still occur. It’s important to be prepared in the case of an emergency situation. Conduct regular fire drills a few times a year and also make sure to supply employees with safety training according to both federal and state standards. Make sure to have an assigned meeting point for all employees to account for each person after the drill.
Employee training is just one step of this process though. Make sure that emergency phone numbers and any firefighting equipment are accessible and understood by employees. Keep the fire extinguishers up to date and in good working condition. Make sure that each employee understands the building’s evacuation strategy from their initial start at the company. A public address system is also a good idea and can be used to inform personnel in case of an emergency. The emergency exits should be marked and easy to reach. Finally, local fire departments are great resources for local businesses. They can provide valuable information on how to react in a fire and also if the building has done an adequate job of preparing for a fire.
Final Thoughts
Workplace fire accidents are known for their catastrophic loss of human life as well as equipment and materials. When it comes to safety and security, prevention is the key. From focusing on simple steps like cleaning to building an evacuation plan, these basic safety tips will help to keep your workplace security. Keeping workers safe is an important part of managing risk to keep your Worker’s Compensation insurance premiums low. If you need help evaluating your risk profile be sure to reach out to us.
by jeffp | May 16, 2017 | Workplace Safety

Consider your work chair. Is it comfortable and also supportive? Do you feel healthy being in it? Is it steady?
If you responded to “no” to any of these questions, you could need a new chair– one that is ergonomically correct. But it is essential for your company and you to do the research initially. “There are lots of ergonomic chairs available, however it can be a blunder to purchase one simply since it is labeled ‘ergonomic,’”
Some ergonomic chairs are more expensive than others but what matters is that the chair fits the person. According to the Canadian Center for Occupational Health & Safety, a chair ends up being ergonomic only when it:
- Particularly suits an employee’s dimensions,
- Their desk, and
- What work they do there.
The ideal chair is flexible:
- Can the seat height be adjusted? It’s really important that a seat elevates an employee to the correct height.
- Is the backrest adjustable? It needs to have the ability to be changed both vertically as well as in frontward and also backward directions. In addition, the chair should have a company lumbar support.
- Does the chair have a seat deepness appropriate for the worker?
- Is the chair stable? Having a chair with a five-point base is best.
Finding a chair that fits:
Office workers spend the bulk of their time sitting… and sitting incorrectly can lead to injuries. So to have a great chair that fits, take these variables into consideration:
- Understand that chair won’t always help every worker.
- Make sure the chair seat elevation is 1/4th the worker’s elevation, but also make sure it fits the employee’s leg-to-torso ratio.
- The same chair is not always ideal for all activities. Be prepared to have different types of chair in your environment that are task and worker specific.
- Some are surprised to learn that chairs require maintenance. Be sure to check with the manufacturer for what possible issues may arise.
- Be sure to allow users an opportunity to try and compare chairs. After all, they will be the ones using the chairs on a daily basis.
It may surprise you, but many workers’s compensation claims are related to poor ergonomics.
Millions of workers suffer work-related musculoskeletal disorders each year. Hundreds of thousands miss work as a result. Shockingly $1 of every $3 spent on worker’s comp claims is from inadequate ergonomic protection. Total annual costs for these types of claims exceed $45 billion each year.
The best “cure” for these situations is simple prevention. An investment in ergonomic chairs is far better than the claims that could result from poor seating for your workforce.
Have questions about ergonomics and their impact on worker’s comp claims? Be sure to reach out to your worker’s compensation insurance professional for answers!
by jeffp | Mar 14, 2017 | Workplace Safety

When one thinks of places to run into electrical hazards, the office isn’t the first place that comes to mind. Injury from falls is certainly #1 on the list of risks. #2 comes from lifting heavy object.
Certainly folks that deal directly with electricity are far more likely to suffer potential injury. 20% of all electrical injuries (shocks & burns) occur with Electricians and apprentices. Meanwhile 12% of all electrical injuries happen to Mechanics. But according to the Bureau of Labor Statistics, 35% of all electrical injuries occur to the “other” category of worker that includes folks who work in offices.
In fact OSHA published a guide in 2002 to help understand electrical hazards and how to minimize their risks.
Here are some basic guidelines to help eliminate electrical shocks & burns in the office…
- Make sure all devices are shut off before leaving the office at the end of the day.
- It’s best to use devices that are grounded. (They have a 3-prong cord.) Be sure that they are plugged into 3-prong outlets.
- If a device is giving off an unusual smell… like plastic burning… unplug it right away.
- Never work with devices that have damaged cords.
- Be sure that all walkways in the office are free from extension cords.
- Never use staples or nails to try and position electrical cords.
- Never plug devices into outlets that have a loose connection.
- Only use devices that have passed independent screening such as by Underwriters Laboratories.
- Ensure that there’s a 3’ clearance in front of electrical panels, transformers, etc.
- Never connect devices to an electrical outlet through a series of electrical extension cords.
Most of these may seem like common sense but they should be incorporated into worker safety training. Not only will they reduce worker injury risks from shocks, they can also help to eliminate potential electrical fire risks as well. And while you are at it, be sure to talk with your insurance professional for other ideas on how to keep your workers safe as well.
by jeffp | Dec 30, 2016 | Workplace Safety
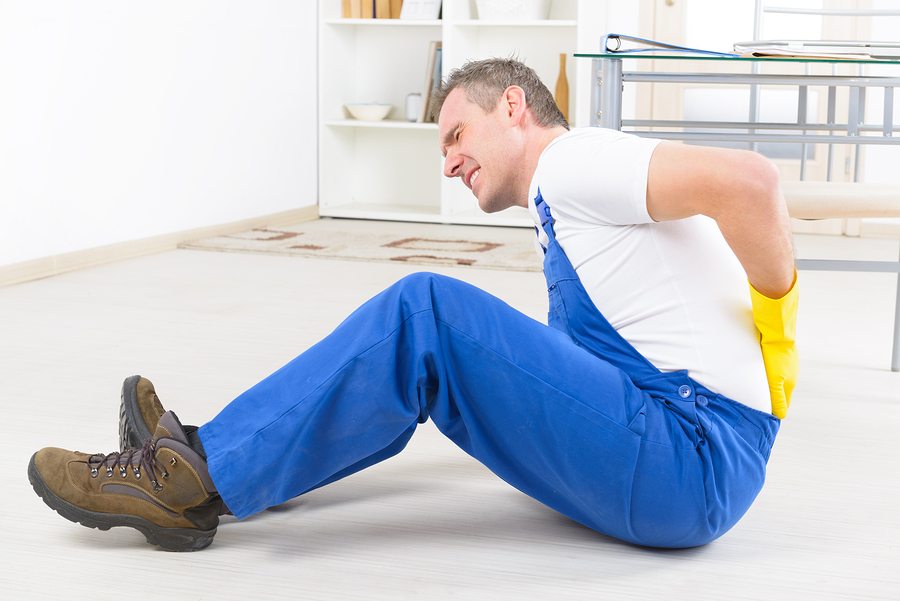
Injuries can occur at any workplace—from minor sprains and strains to life-altering amputations—and happen more frequently than you may imagine. According to data from the Bureau of Labor Statistics (BLS), nearly 3 million nonfatal workplace injuries and illness were reported by private industry employers in 2014. Another 722,300 (estimated) employee injuries and illness were reported by state and local government employers.
While illnesses and injuries on the job can happen in any industry, those with the highest percentage are local government transportation and warehousing; local government justice, public order and safety; state government healthcare and social assistance; local government construction; and local government trade, transportation and utilities. Within these industries, between 2.7 and 4 percent of employees suffered an injury or illness in 2014.
Employees in private industries fared better. Most of the industries with the lowest percentage of reported injuries and illness were in the private sector. They include professional, scientific and technical services reporting (with the lowest injury and illness rate of any industry, private or government); management, financing, professional services; and state government educational services. Within these industries only 0.25 to 0.6 percent of employees suffered a reported injury or illness in 2014.
Of course, some injuries and illnesses are more serious than others, requiring employees to spend more time away from the job while they recover. Some industries with average illness and injury rates are still more heavily impacted by these events than those with higher rates because of the recovery time associated with the injuries their employees sustain.
The BLS data show that the top five industries in terms of days away from the workplace are mining (with an average of 31 recovery days per incident); local government transportation and warehousing (21); private sector transportation and warehousing (20); local government trade, transportation and utilities (16); and state government justice, public order and safety (14).
Industries in which reported illnesses and injuries require employees to spend the fewest days away from the workplace while recovering are educational services (5 days on average); accommodation and food services (6); agriculture, forestry, fishing and hunting (6); education and health services (6); and healthcare and social assistance (6).
The age of employees who suffer workplace illnesses and injuries appears to have an effect on the number of days they need to recover away from the job—regardless of industry. While the data shows injured workers between the ages of 20 and 24 spend an average of 5 days recovering, that number jumps to 6 days for workers between the ages of 25 and 34, and then skyrockets to 10 days for workers who are 35 to 44. Injured employees between the ages of 45 and 54 need an average of 12 days away from their job, while those 65 and older need the most time—17 days on average.
By now you’re probably wondering which workplace injuries and illnesses are most common. The BLS keeps track of that as well. For 2014, their data shows that sprains, strains and tears top the charts, followed by musculoskeletal disorders (including tendonitis and carpal tunnel syndrome), soreness and pain, bruises and contusions, cuts and lacerations, and fractures.
What events are most likely to cause these injuries and illnesses? Overexertion and bodily reactions are the major contributor, followed by falls, slips and trips; contact with object or equipment; violence and other injuries by person or animal; transportation incidents; exposure to harmful substances and environments; and fires and explosions.
Regardless of your industry, it’s your responsibility to provide your employees with a safe workplace and do what you can to reduce their chances of sustaining a work-related injury or illness. A comprehensive safety program—including regular, consistent jobsite training—is essential, as is a period review to ensure your program is adequately addressing developing issues.